Five Ways to Make Your Supply Chain More Dynamic Part 1: Follow Actuals, Not Averages
- Michael Intravartolo
- Apr 27, 2016
- 2 min read
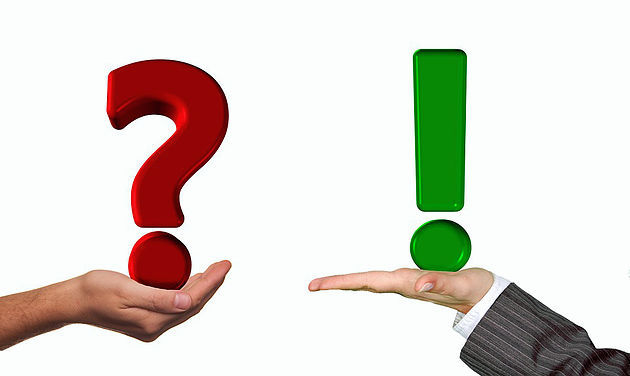
Keeping tabs on your company’s supply chain is no small task when you’ve got hundreds if not thousands of bits of data whirling by as materials come in the door and finished goods go out. To stay on top of it all, you and your team need an efficient system that can automate processes and keep you informed with accurate data that’s easy to get your hands on. In this series of supply chain management (SCM) blogs, we’ll show you how to get a better handle on the details, adapt when things don’t go according to plan, turn your data into insight, embrace change, and share ideas. Let’s get started with how to go beyond guesstimating.
Follow Actuals, Not Averages.
Tracking costs through your supply chain to get a true sense of what it takes to go from raw materials to delivered product is very necessary, but without the right tools it can be difficult, if not impossible. And traditional approaches to creating and tracking this total landed cost are often based on estimates of numerous individual costs—from average fuel prices to median postage and delivery charges—that make up your total. As a result, your total costs can be anything but accurate.
Getting a real look into real costs from across your supply chain lets you make educated adjustments to pricing, marketing and sales. And that can have a real impact on profitability.
Microsoft Dynamics NAV lets you track landed, standard and perpetual costs, so you have a more accurate view of every product that leaves your facility and lands at a customer’s door. From your standard reports, you can drill down to more specific details like costs by warehouse location.
And by connecting your supply chain, financial management, sales and marketing functions, you can run item-by-item profitability analysis across your supply chain and help your sales teams and marketers prioritize the products, locations and types of customers that deliver the greatest profitability.
Plus, Microsoft Dynamics NAV provides better audit trails for tracking cost adjustments, so you can ensure changes are recorded, tracked and, of course, fed directly into your financial management process.
Next time, we’ll close out our series by talking about planning for the unexpected disruptions that could grind your supply chain to a painful halt, but until then, read how fashion company Dixie uses Microsoft Dynamics to solve cumbersome pricing processes, or see the product in action and learn about packaged pricing.
Comments